The textile industry has seen significant advancements in automation, enabling faster production, higher precision, and improved efficiency. One of the key components driving this transformation is the electric linear actuator. These actuators provide controlled linear motion, replacing traditional pneumatic and hydraulic systems with a cleaner, more reliable, and energy-efficient alternative.
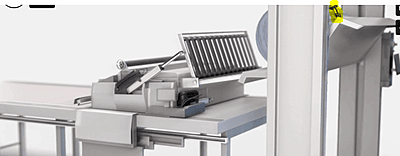
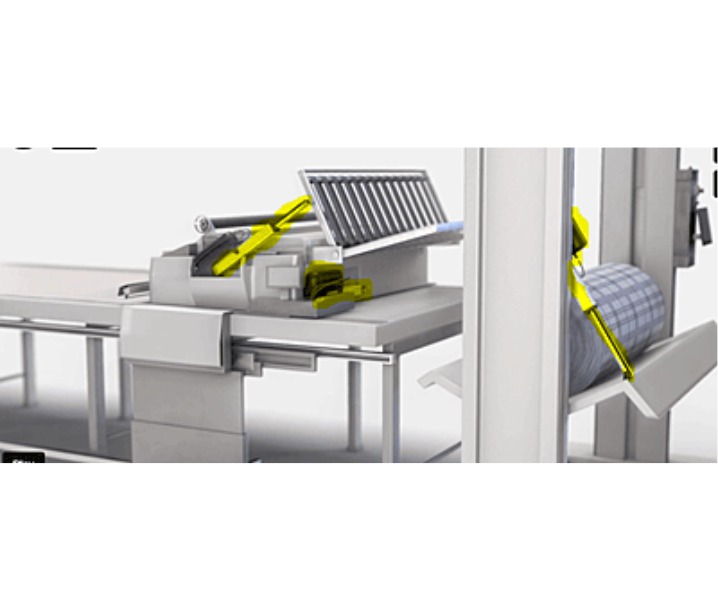
Why Linear Actuators in Textile Machines?
Textile manufacturing involves multiple stages, such as spinning, weaving, dyeing, and finishing. Each of these processes requires precise movement and positioning of fabric, rollers, and cutting mechanisms. Electric linear actuators play a crucial role by offering:
Precision & Repeatability – Ensuring accurate movement in fabric handling and pattern cutting.
Energy Efficiency – Consuming less power compared to hydraulic and pneumatic systems.
Low Maintenance – Eliminating leaks and frequent servicing associated with hydraulic actuators.
Clean & Eco-Friendly Operation – No risk of oil spills, making them ideal for fabric processing.
Applications of Linear Actuators in the Textile Industry
1. Weaving Machines
Weaving is a critical stage in textile production that requires smooth and precise fabric movement. Linear actuators are used to control the shuttle movement, adjust fabric tension, and ensure uniform weaving, reducing errors and enhancing quality.
2. Dyeing & Finishing Lines
During the dyeing process, fabric needs to be handled with care to ensure uniform color application. Linear actuators help adjust roller pressure, control fabric positioning, and maintain tension, preventing defects. In finishing lines, actuators assist in processes such as coating, laminating, and drying.
3. Cutting & Sewing Automation
Precision is key in cutting and sewing processes. Electric actuators enable automated fabric cutting machines to achieve millimeter-level accuracy. In sewing automation, they help in controlling stitch length, fabric feeding, and pressure adjustments for different materials.
4. Material Handling Systems
Large textile factories require efficient handling of fabric rolls, reducing manual labor and increasing productivity. Linear actuators assist in roll unwinding, tension control, and robotic material handling systems to streamline production.
Advantages of Electric Actuators Over Pneumatics
Many textile industries are now shifting from pneumatic actuators to electric actuators due to: Higher Energy Savings – No air compressors required, reducing energy consumption.
Better Control & Accuracy – Smooth, adjustable speeds for delicate fabric handling.
Longer Lifespan & Durability – Less wear and tear, reducing downtime and maintenance costs.
Eco-Friendly Operation – No oil leaks or air pressure fluctuations affecting production.
Integration with Industry 4.0 in Textiles
The future of textile manufacturing is driven by Industry 4.0, where smart automation plays a key role. IoT-enabled electric actuators allow manufacturers to:
Monitor machine performance in real-time
Enable predictive maintenance to reduce downtime
Optimize fabric tension and movement through AI-driven analytics
Reduce manual intervention, leading to consistent product quality
Case Study: Linear Actuators in an Indian Textile Plant
A leading textile manufacturer in India recently upgraded its weaving and dyeing lines with electric linear actuators. The results:
30% increase in production efficiency
20% reduction in energy costs
Significantly lower machine maintenance
Improved fabric quality and reduced wastage
Conclusion
As textile industries embrace automation, electric linear actuators are becoming a game-changer. Their precision, reliability, and efficiency make them an ideal solution for modern textile manufacturing. If you want to enhance your textile production with clean, cost-effective, and highly efficient automation, electric actuators are the future.